 |
|
Experimental results of field test vehicles
The results demonstrated in the following paragraphs have
been achieved within the INTEROP joint research project by scientific
lab tests and field test operation.
Vehicles and secondary pads
One of the most important special features of the WiPT-standard
interoperability definition is the ability to design mechnical and
magnetically different secondary pads exactly adjusted for the desired
vehicle. Nevertheless, all of them can be operated on a
standardized magnetic energy source, the primary pad.
Design roules are provided to adjust the secondary pads to different
mechanical space and ground clearences required by different vehicles.
To demonstrate and to verify this feature of mechanical flexibility of
the interoperability definition four different vehilcles have been
equipped with very different secondary pads. Especially concerning the
pad size extremely different pad have been designed which are listed in
the following table together with the vehicles at which the pad are
used. Intense scientific research has been executed at the first three
vehicle types A to D, whereas C and D distinguished same mechanical and
electrical designes prduced by two different manufacturers.
|
Pad / vehicle B2
|
Pad / vehicle A
|
Pad / vehicle C/D
|
Pad / vehicle E
|
Secondary coil type
|
Double flat
|
Double flat
|
Solenoid
|
Solenoid
|
Sekundäre Feldplatte
|
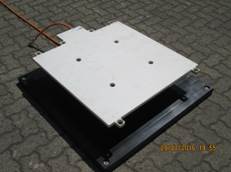
|
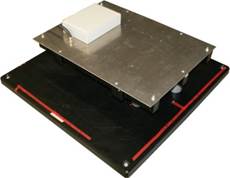
|
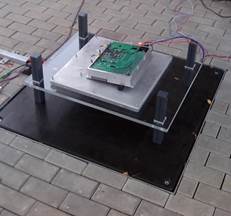
|
|
Vehicle type
|
iMiEV / eOn
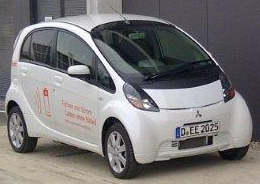
|
Streetscooter B14
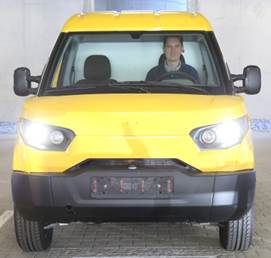
|
Cetos (based on Opel
Corsa)
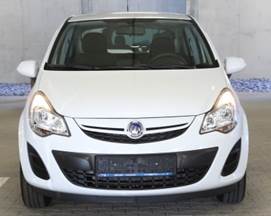
|
Karabak (based on
Fiat 500)
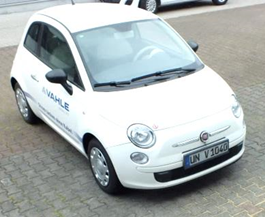
|
A further vehicle indicated with B1 has the same vehicle type as C and D but carries the secondary pad desing of vehicle B2.
Therefore one single vehicle type carries pads of very differnt sizes
and different coil topologies (double flat and solenoid) thus enabling
a direct comparison of the pad designs.
The differences are stated more precisely in the following table,
listing the most important technical parameters of the experimentally
investigated pads. Apart from different pad sizes the broadly different
battery voltages should be noted, also. For the supply device (primary
charging pad) the varying nominal battery voltages do not make
any difference in its functionality. This feature is similar to AC
charging as in this case the vehicle mounted charger adjusts the line
voltage to the battery voltage. For DC charging this feature is quite
inpossible (or at least technically not desireable) used for fast
charging as the charger is located outside the car and cannot
specifically designed for different DC voltages.
Secondary pad
|
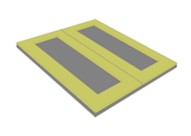
|
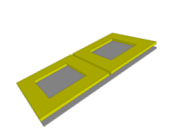
|
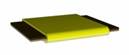
|
Application
|
Vehicle B1
|
Vehicle A
|
Vehicle C/D
|
Coil type
|
Double flat
|
Double flat
|
Solenoid
|
Case size
(length*width)
|
750 * 750 mm2
|
700 * 500 mm2 |
750 * 750 mm2 |
Ground clearance
|
150 mm
|
156 mm
|
146 mm
|
Battery voltage
|
400 V
|
140 V
|
380 V
|
Coupling factor
|
0,28
|
0,27
|
0,25
|
Coupling
(magnetic conductivity of the coupling flux)
|
203 nH |
205 nH
|
166 nH
|
Secondary current linkage (current * winding turns)
[Primary current linkage: 120 A]
|
154 A
|
239 A |
318 A |
Despite of these lage varying constructive, magnetic and electrical
differences all pads and vehicles are able to charge on the primary
pads of the supply devices although these primary pads have been
produced by two different manufacurers. This is possible as both
products are fulfilling the WiPT-standard.
This manufacturer independent interoperability is exemplarily
demonstrated by the following figure showing Components of all involved
technology manufacturers.
Experimentally measured transferred power and efficiency
During a cross exchange test of all possible twelve
combinations of tree supply devices and four vehicles the features of
mixed operation have been measured and verified. Despite the two
operational supply devices shown in the previous figure the third
supply device is the primary reference device build for certification
and lab measurement purposes. This reference device is exactly
constructed according to the mechanical and electrical requirements of
the WiPT-standard.
The operational devices vary in the coil design from the reference
device due to manufacturer specific additional features and production
needs but still fulfill the basic interoperability definition just
specifying the current linkage balance. For that reason the cross test
also proves the choice of defining the current linkage balance as
sufficient and not limiting the interoperability.
The proof of interoperability in the sense of
guaranteeing energy transfer the left figure shows the measured power
for all combinations of the cross test. The measured power is the power
at the DC terminals of the battery being the relevant parameter for a
charging process. For all combinations 3 kW power is reached thus
proving the desired feature of interoperability. The visible difference
must not be interpreted as quality differences of the design, rather
they result from differnt desired operation parameters being variable
and free of choice.
The operative supply devices implement an automatic setpoint tracing of
the primary current linkage to exactly transfer a choosable setpoint of
power drawn from the grid. The two operational supply devices have
slightly different setpoints. But due to the setpoint tracing parameter
variations due to the four different vehicles are compensated and each
vehicle receives the same power on a single supply device. In
contradiction the reference supply device does not implement the
setpoint tracing and is operated exactly at the nominal primary current
linkage value. Due to difference between design consiiderations and
practical operation the operation point of transmitted power varies
between the different vehicles. Reasons might be a not exact
positioning of the vehicle or variance of the ground clearance due to
vehicle loading.
Additionally, the graph on the right side shows
the efficiency of the energy transfer also for all combinations of the
cross test. The efficiency is measured between the battery terminals
and the grid connection point (wall plug). All combinations, even the
combinations of manufacturer mixed operaton, reach an efficiency of
nearly 90%. Surprisingly for the technology manufacturers the
efficiencies do not significantly differ between all combinations
although very different designs of secondary devices have been used.
|